Finance for Operations Managers
Finance for Operations Managers
Skills you’ll gain
Tailored towards operations managers seeking to boost their financial skills to improve their organization’s performance, this online course will help you understand how your decisions can improve efficiency, drive successful projects, and impact the financial performance of the business.
Highlights:
- 35 lessons
- Understand the fundamental financial concepts in business and their uses.
- Interpret data on financial reports and how these reports impact each other.
- Understand how budgets and estimates are used to plan and control costs.
- Utilize ratios and measures to gain insight into profitability and performance.
- Analyze cost behavior, track operational expenses, report on cost variance and forecast expenses.
- Delve into operations finance principles: product cost, inventory cost management, make versus buy
- Earn 14 contact hours or PDUs toward your project management education for certification with PMI.
The Finance for Operations Managers course builds on the 16 lessons from the Finance for Non-Financial Professionals course with an additional 19 lessons focused on Operations Managers.
Once enrolled, our friendly support team and tutors are here to help with any course related inquiries.
Syllabus
Download syllabus-
1
Earnings Statement Part 1 The Earnings Statement is a financial report that shows business profitability over some time period. 4m
-
2
Balance Sheet Part 1 The Balance Sheet is the financial report that shows what the business is worth at some instant in time. 6m
-
3
Cash Flow Statement Part 1 The Cash Flow Statement is a financial report that shows how well the company was able to convert business activity into cash over some time period. 5m
-
4
Relationships Between Financial Statements Each of the financial statements provides insight on an aspect of the business financial status and structure. These accounts across the statements are related, and changes to values will likely impact multiple statements. 4m
-
5
Earnings Statement Part 2 The Earnings Statement is a financial report that shows business profitability over some time period. This lesson will focus on the revenue portion of the Earnings Statement. 5m
-
6
Earnings Statement Part 3 The Earnings Statement is a financial report that shows business profitability over some time period. This lesson will focus on the expense portion of the Earnings Statement. 5m
-
7
Balance Sheet Part 2 The Balance Sheet is the financial report that shows what the business is worth at some instant in time. This lesson will focus on the Asset side of the Balance Sheet. 4m
-
8
Balance Sheet Part 3 The Balance Sheet is the financial report that shows what the business is worth at some instant in time. This lesson will focus on the Liabilities and Equity side of the Balance Sheet. 4m
-
9
Cash Flow Statement Part 2 The Cash Flow Statement is a financial report that shows how well the company was able to convert business activity into cash over some time period. This lesson will focus on sources of cash. 5m
-
10
Cash Flow Statement Part 3 The Cash Flow Statement is a financial report that shows how well the company was able to convert business activity into cash over some time period. This lesson will focus on uses of cash. 5m
-
1
Profit Measures When calculating profitability, the different profit measures provide insight into the most significant factors that are creating corporate profit or loss. 4m
-
2
Return on … Ratios Return ratios are normally used for comparing companies or comparing the past performance of a company with its present performance. 4m
-
3
Working Capital Measurements The working capital and turnover measurements are used by operations managers to track the efficiency of the operations. 4m
-
1
Cost Account Characteristics It is important to know what category of account you are working with when budgeting and tracking spending. The different categories of accounts behave differently so knowing which category you are working with will provide insight into the budgeting and tracking process. 5m
-
2
Estimating Estimating is used when planning and budgeting business costs or revenues. The estimate needs to include both the amount and the timing of the transaction. 5m
-
3
Capitalization and Amortization Whenever a company purchases an asset with long term value, it must be capitalized. Every asset that is capitalized is then depreciated, which is special form of amortization. 4m
-
4
Depreciation If you capitalize a fixed asset, you are required to depreciate it on the business financial books. 5m
-
5
Budget Baseline Budget baselines should be used if costs must be controlled within a department or on a project. 4m
-
6
Strategic Planning and Budgeting Most businesses prepare a strategic plan that projects how the company will achieve or maintain a competitive advantage. It is used to guide the budgeting process. 4m
-
7
Business Budgeting Business budgets are the financial plan of the business. They are normally created for one year at a time and allocate the spending and revenue across business units, departments and accounts. 5m
-
1
Developing a Business Case The business case provides the business rationale, normally in financial terms, of why a project should be done. 5m
-
2
Return on Investment (ROI) Return on Investment is a financial calculation to determine whether the business benefit of an investment is worth the cost. 5m
-
3
Payback Period The Payback Period is a Return on Investment analysis that determines the amount of time needed to accumulate enough benefit to pay for the cost of the project. 5m
-
1
Cost Behavior The business financial system records costs based upon the cost account type. The costs are often accrued near the end of fiscal quarter or year. 5m
-
2
Cost Variance Reporting Cost variance reporting is the calculation and reporting of costs that are different than what was expected by the budget or standard. 5m
-
3
Tracking Operational Expenses Operational expenses are the normal costs of the business and are tracked by function and cost type. They are either reported as totals on a per unit (unit cost) basis. 4m
-
4
Forecasting Expenses Financial forecasts for the final cost of activities are created to allow activity managers to make wise business decisions. The approach used for forecasting should vary based upon the nature of the activities being forecasted. 5m
-
1
Product Cost The business circumstances will dictate how best to analyse and assess product cost. Factors to consider are the manufacturing location, material and labor content, and product configurations. 5m
-
2
Inventory Cost Management Companies that manufacture products must manage their inventory to keep costs low but availability high. 5m
-
3
Make versus Buy Make versus Buy is a decision process to determine if a product, or part of a product, should be made by the company or by a supplier. 4m
-
4
Productivity Productivity is a term used to indicate improved efficiency which results in more output for the same input. 5m
Certificate
Certificate of Completion
Awarded upon successful completion of the course.
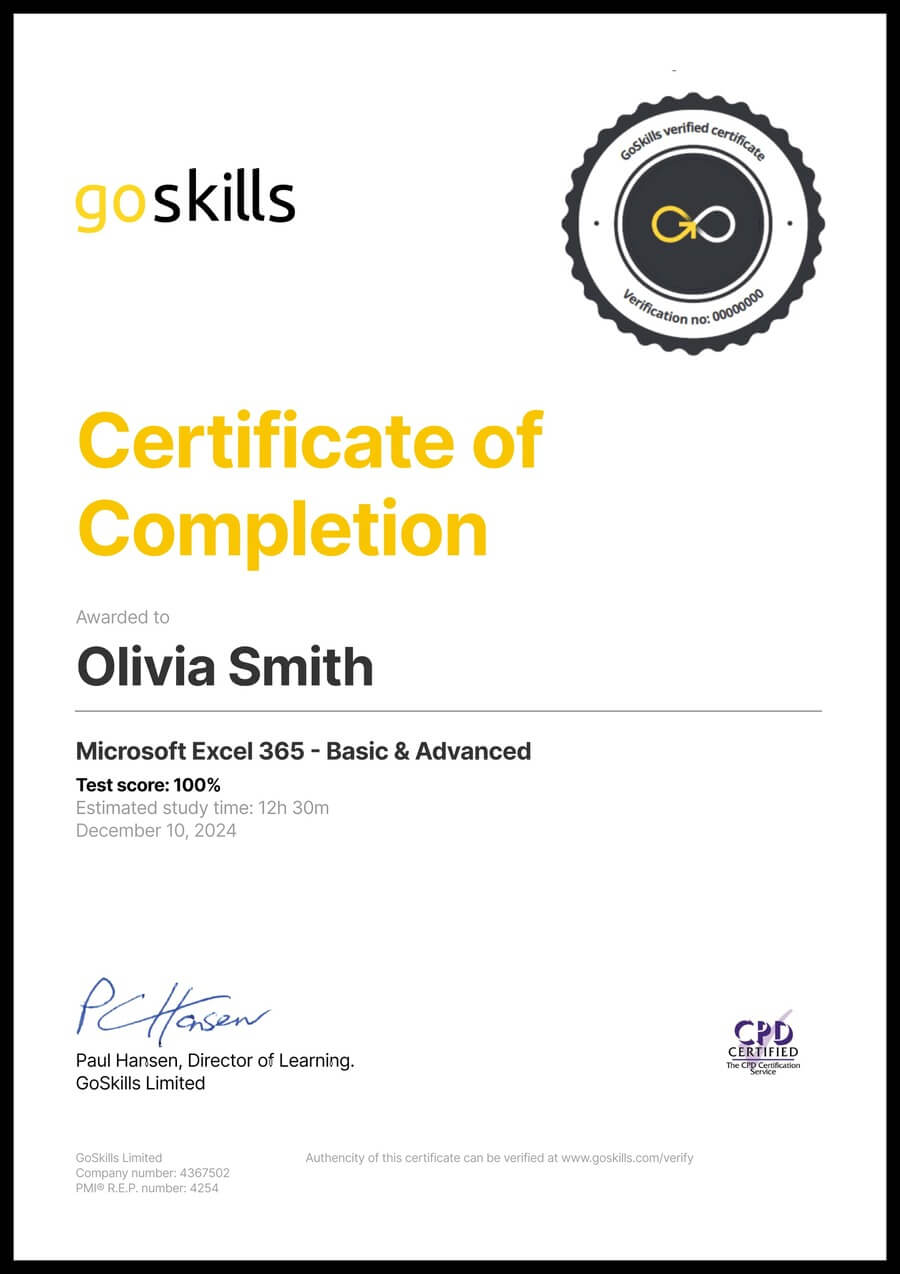
Instructor
Ray Sheen
Ray is a certified Project Management Professional (PMP) with the Project Management Institute, a certified Scrum Master with Scrum Alliance, and certified Lean Six Sigma Black Belt with IASSC. He is a member of the Project Management Institute and the Product Development Management Association.
He is president and founder of Product & Process Innovation, Inc. and is a veteran business leader with over 25 years of executive, project management, and engineering management experience. Ray has worked in several industries including aerospace, electrical distribution and utilities, biotechnology, appliances, electronics, machining, medical devices, pharmaceutical, automotive, and financial services. He has held executive management positions in a Fortune 500 company and has been involved in entrepreneurial startup organizations.
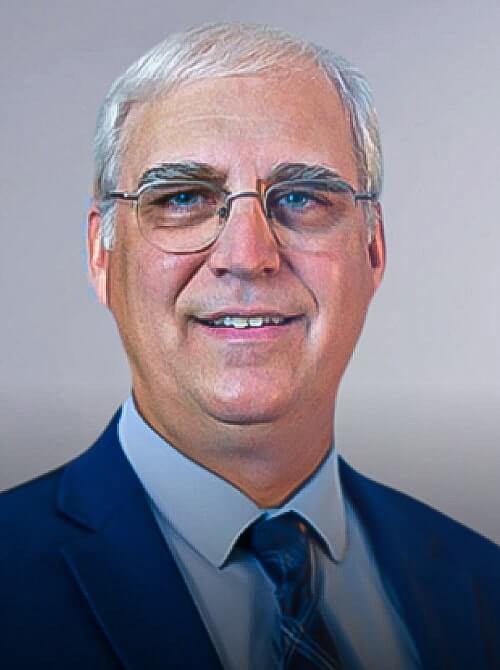
Ray Sheen
Project Management Instructor & Author
Accreditations
Link to awards The PMI ATP seal, PMI, PMP, CAPM and PMBOK are registered marks of the Project Management Institute, Inc.How GoSkills helped Chris
I got the promotion largely because of the skills I could develop, thanks to the GoSkills courses I took. I set aside at least 30 minutes daily to invest in myself and my professional growth. Seeing how much this has helped me become a more efficient employee is a big motivation.
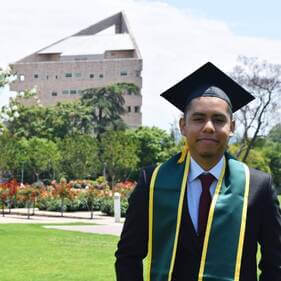