Measurement Systems Analysis Training | Online Course - GoSkills.com
Measurement Systems Analysis
Skills you’ll gain
This course is part of our Lean Six Sigma Green Belt program, which consists of four courses designed to prepare you for the International Association of Six Sigma Certification (IASSC) Green Belt exam. We recommend you take all four courses in the program to be fully prepared for the exam.
Measurement systems analysis helps you understand how much variation is present in your measurement system. When you’re driving your car and the fuel gauge shows ¼ of a tank remaining, you want to be able to trust that measurement is correct. The same is true of any measurement system you use in your business.
In this course you will learn how to apply the vital techniques of measurement systems analysis in your business processes. The analysis will tell you if your measurement system is capable of accurately and consistently providing data that reflects the true condition of products and processes in your business.
The training features plenty of opportunities to practice with examples, exercises and quizzes to test your knowledge. By the end of the course, you will have the skills to conduct simple, straightforward analysis to understand uncertainty in measurement systems and improve processes at your company.
You won’t need to do any advanced math or derive proofs behind the formulas or statistics. You will learn how to use popular programs like Excel and Minitab to do the calculations, and how to read the data and analyze the results of the study.
Highlights:
- 12 practical tutorials with videos, reference guides, exercises and quizzes.
- Designed to prepare you in part for the IASSC Green Belt exam. To prepare in full, you should also take the Lean Six Sigma Principles, Statistical Process Control, and Hypothesis Testing courses part of our four course Lean Six Sigma Green Belt program.
- Understand the concept of a data measurement system and data measurement error.
- Learn the key attributes of an effective data measurement system.
- Master the Gage Repeatability and Reproducibility (Gage R&R) technique to understand the typical variation that exists in your measurement system.
- Perform Variable Data and Attribute Data Gage R&R calculations using Excel and Minitab.
- Aligned to the IASSC Lean Six Sigma Green Belt Body of Knowledge.
- The only method to earn an IASSC certification is to successfully sit for and pass an official IASSC certification™ exam, which can be taken through IASSC. We do not provide access to IASSC Certification exams.
- Earn 2 PDUs or contact hours toward your Project Management education for certification with PMI.
Once enrolled, our friendly support team and tutors are here to help with any course related inquiries.
Syllabus
Download syllabus-
1
Gage R&R Principles Gage R&R studies are the best practice for determining measurement system process capability and maintaining that capability. They quantify the level of precision that the measurement system will deliver. Key principles for conducting effective Gage R&R studies are introduced in this lesson including those for managing the appraisers and for selecting the items for measurement. 6m
-
2
Gage R&R Methodology This lesson describes a step by step process for planning and conducting a Gage R&R Study. It includes templates for data collection for both variable data studies and attribute data studies. 7m
-
3
Gage R&R Study Design Considerations When designing the study, there are several critical considerations based upon the type of test (destructive or non-destructive), the discrimination of the test system, and whether attribute tests can designate an item into multiple categories beyond Pass/Fail. These considerations impact the accuracy and performance of the analysis. 7m
-
4
Gage R&R Execution and Analysis This lesson reviews best practices for executing the Gage R&R Study plan. It also explains how the results are presented for both variable data Gage R&R studies and attribute data Gage R&R studies. This includes presenting the target values of acceptable measurement system performance. 5m
-
5
Variable Data Gage R&R Calculations Variable data Gage R&R Studies calculate a comprehensive measurement that can be used to determine the efficacy of the measurement system that is creating variable measurements of product or process characteristics. This lesson describes those calculations and highlights where weaknesses in the system will be exposed. 7m
-
6
Variable Data Gage R&R Examples This lesson walks through an example of a variable data Gage R&R analysis. The example is demonstrated using manual data collection and equations with a spreadsheet in Microsoft Excel. The same example is then demonstrated using the statistical software program Minitab, which is often used to conduct analyses for Lean Six Sigma projects. 6m
-
7
Attribute Data Gage R&R Calculations Attribute data Gage R&R Studies generate a number of metrics that are used for judging the performance of the measurement system used to evaluate pass/fail attribute data. In this lesson, each of these metrics is described and the method of calculation is explained. 7m
-
8
Attribute Data Gage R&R Examples This lesson walks through an example of an attribute data Gage R&R analysis. The example is demonstrated using manual data collection and equations with the Microsoft Excel spreadsheet application. The same example is then demonstrated using the statistical software program Minitab, which is often used for analyses with Lean Six Sigma projects. 6m
-
9
Type 1 Gage Studies Gage R&R studies can be done with automated test equipment to be certain that they are providing accurate and precise results. These are known as Type 1 Gage studies. These studies can be used with any type of automated checking or testing system, not just manufacturing systems. A satisfactory Type 1 Study is often needed to convince stakeholders to have confidence in automation. 5m
Certificate
Certificate of Completion
Awarded upon successful completion of the course.
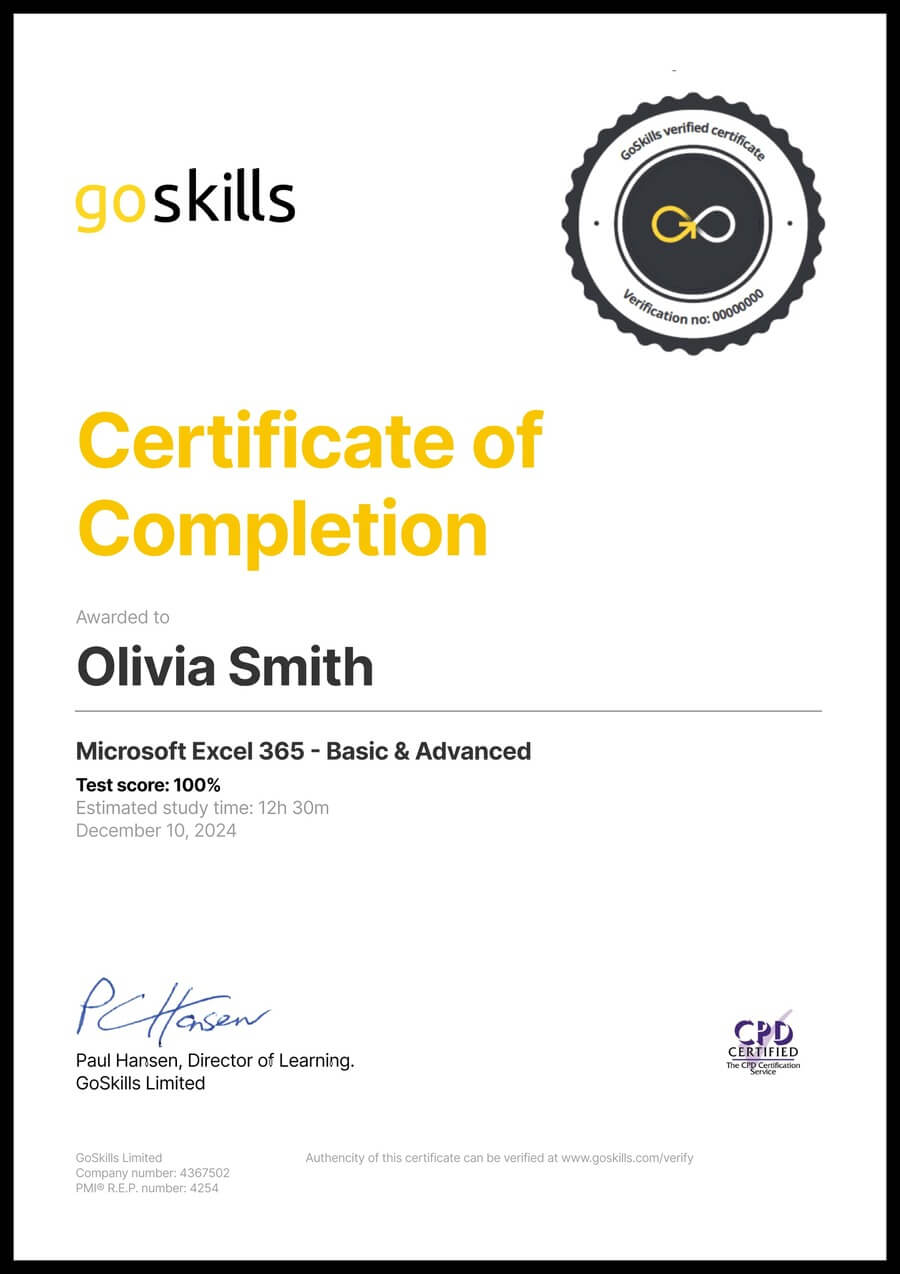
Instructor
Ray Sheen
Ray is a certified Project Management Professional (PMP) with the Project Management Institute, a certified Scrum Master with Scrum Alliance, and certified Lean Six Sigma Black Belt with IASSC. He is a member of the Project Management Institute and the Product Development Management Association.
He is president and founder of Product & Process Innovation, Inc. and is a veteran business leader with over 25 years of executive, project management, and engineering management experience. Ray has worked in several industries including aerospace, electrical distribution and utilities, biotechnology, appliances, electronics, machining, medical devices, pharmaceutical, automotive, and financial services. He has held executive management positions in a Fortune 500 company and has been involved in entrepreneurial startup organizations.
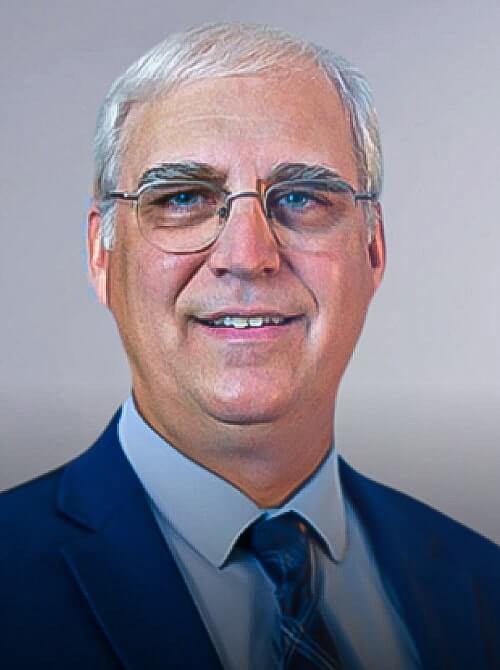
Ray Sheen
Project Management Instructor & Author
Accreditations
Link to awards GoSkills Ltd is an IASSC Accredited Training Organization™. The PMI ATP seal, PMI, PMP, CAPM and PMBOK are registered marks of the Project Management Institute, Inc.How GoSkills helped Chris
I got the promotion largely because of the skills I could develop, thanks to the GoSkills courses I took. I set aside at least 30 minutes daily to invest in myself and my professional growth. Seeing how much this has helped me become a more efficient employee is a big motivation.
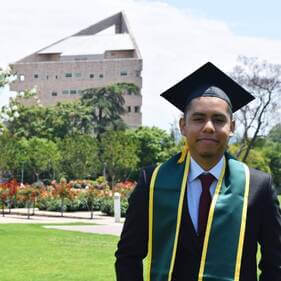