What is 5S?
5S is a mnemonic for remembering the five pillars of the visual workplace. In a visual workplace, visual cues — from signs to prepared kits — show people how to carry out operations productively and safely.
The following list of steps gives the short words or phrases that give 5S meaning:
Want to learn more about the Lean Six Sigma methodology?
Check out this ebook that will guide you through the key concepts of LSS.
Implementation of a visual workplace is a way to attain the common goals of Lean Six Sigma, such as reducing the 8 wastes and improving quality.
The visual workplace that 5S methodology is meant to enable has roots going back centuries. However, the current form is usually considered to have been part of the evolution of the Toyota Production System (TPS) following the second world war.
5S is usually undertaken as part of a larger initiative, such as a Lean or Lean Six Sigma project. In the modern era, 5S initiatives have expanded beyond their manufacturing roots. Lean and 5S are practices that have achieved successes in many different industries, including health care, agriculture, and finance.
There are few contexts where the principles of 5S can’t make a business more efficient.
Benefits of 5S
Lean undertakings that implement the 5S methodology are not without effort, so the benefits should be clear before you begin — and explained to all of the people that you’ll need to involve.
The primary benefits of a 5S system are shared with other Lean tools. Generally, you’ll undertake the implementation of a 5S system because you’re motivated to achieve one or more of the following:
- Increased productivity
- Fewer defects
- Decreased waiting times
- Increased workplace safety
5S examples
Examples of these benefits are easy to find. While it might be easy to intuitively think that a workplace where what you need is always close at hand will be more productive, consider some of these more concrete examples.
- Swarnkar and Verma (2017) show a 31 percent improvement in productivity at a small business manufacturing corrugated cardboard boxes.
- Ebuetse and Dogget (2018) show a 12 percent reduction in the time needed to find equipment at a university lab.
- Rees (2010) documents a reduction in nurse’s daily time checks of 175 hours per year in an emergency room department.
- Gupta and Jain (2014) describe preventing machines from scattering glass chips — sometimes onto the floor, sometimes into other machines, and sometimes directly into operators causing injury.
Each of these studies also includes other benefits from Lean 5S thinking. Another particular benefit that arises in these and many other examples is the increased motivation of employees. It is often the case that people are more inspired to come to work and do their jobs well when the workplace has been made into a place that makes it easier to take pride in their work.
The 5S system
To understand the 5S system and how it can fit into your set of Lean tools, we’ll take a look at each of the five parts of the 5S system in turn. The implementations typically follow the same order, so that the sorting step is always the first one in the 5S system.
Sort
Sort forms the foundation for the other steps in the 5S system. If you haven’t sorted, you don’t have the right materials to set in order, and you’ll spend time shining and scrubbing things that don’t deserve your time and attention. The goal of sorting is to leave behind only the items that are necessary to complete necessary work.
If you follow the 5S system, this is where you’ll be introduced to red tags. A variety of different styles are available from any 5S store online, which can look something like the following:
Use of red tags
The red tags serve a purpose. The ultimate idea behind sorting is to categorize everything in the workspace as necessary or unnecessary, but the answer might not be immediately clear for every item.
For anything that needs time to determine how necessary it is to the workspace, tag the item and take it to an area away from the workspace. If it turns out that the item is not needed, then it won’t be missed while it’s absent. If it turns out that the item is necessary, then it will be missed and can be returned from the red tag area to a good spot in the workspace.
If an item stays in the red tag area, make sure that you also have a plan to permanently dispose of it after a few weeks. If an item really is unnecessary, then you don’t want it to take up space that could be used for productive equipment and activity.
Try a sort example
You can try a quick mental sorting exercise with the image below of a computer with some stationery and notepads.
Imagine that the general task for the workspace is to complete administrative reports for a construction site. The reports are done on the computer, so the computer is necessary. What items in the image might you discard or red tag?
Consider the following list:
- Scratch paper
- Whiteout
- Eraser
- Pencil
- Highlighter
- Box cutter
- Colored pencils
Different people can imagine some ways that some parts might potentially be useful. But I think that we’ll all be able to agree that a box cutter will not help with completing the administrative reports and should be kept somewhere that it can be useful.
Set in order
Only after the workplace contains only necessary items is it useful to start setting things in order. The goal of the second step in the 5S system is to arrange those necessary items that you sorted into the most efficient place to get the work done.
When doing the setting in order step of the 5S system, a common tool is a 5S map. The 5S map starts as a diagram of the workspace, such as a floor plan, and then adds the paths that people take to get their work done.
Because the diagrams can become complex when people have to go to many different places to get their work done, a 5S map is sometimes called a spaghetti diagram.
Example 5S map (spaghetti diagram)
Consider the following example from a restaurant kitchen. First, we’ll look at a 5S map that’s a floor plan of the kitchen where we can see the path that people walk among the essential workstations:
In this hypothetical diagram, some of the heavier lines are from the first oven to the packing table and from the packing table to the food delivery window. Putting things that are frequent trips close together helps to eliminate excess transportation — one of the 8 wastes that Lean projects often target.
The following image shows a 5S map of the same kitchen after the stations are set in order:
Example shadow board
In addition to setting things in order, the creation of a visual workplace means that strong visual cues should be in place. This should be done to show people doing the work where things are and how to move from one place to another.
The following image shows a shadow board that shows where each tool for a work station belongs. The shadow board makes it easy to see when all of the tools are present and to find the tool that is needed.
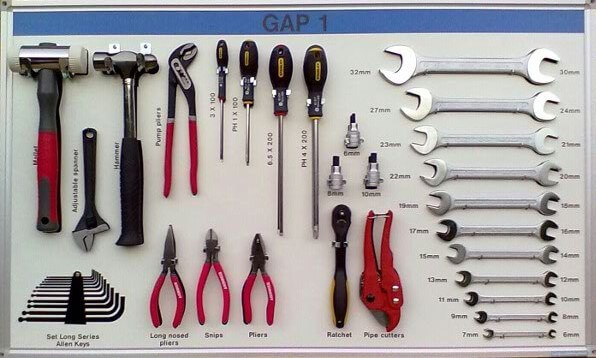
The set in order step is not done until there are visual indicators that make the new order easy to sustain.
Shine
Among the 5S steps, shine can be the most difficult to relate from its abbreviation to what the step involves. While shine implies that cleaning should take place, the completion of the step means more than a one-time cleaning.
As with the set-in-order step, the end includes the creation of a visual plan about how to maintain the shine. In addition, the cleaning and the plan necessitate inspection of spaces and equipment.
If there’s anything that requires attention, then the shining should reveal it so that the proper maintenance can be done — ideally as soon as an issue is noticed. Take advantage of the time in the shine step to consider changes that might make the visuals that you created during the set-in-order step easier to read or see.
Examples of shine
In general, the benefits of the shine step will depend on the industry where you’re applying the 5S methodology.
In a machine shop, the shine step would include both maintaining machines and making an ongoing plan for that maintenance. The maintenance makes sure that the machines are always ready to use and stay in good condition as long as possible.
In a hospital, the shine step would include both sanitizing high touch areas — like remote controls in patient rooms — and making a plan that shows how often someone will sanitize the remote controls going forwards. The sanitizing can reduce the transmission of illness among patients and hospital personnel.
In general, a cleaner workspace should make it easier to find when something is wrong, helping you reduce defects of whatever nature is likely in a particular workplace.
Standardize
Once the first three steps are complete, the standardize step combines the routine activities from all three steps into a more complete plan. The goal of the standardize step is that everything that you need to do to maintain sorting, order, and shining is planned.
Sorting might be done daily, as people remove unnecessary items from the workplace. People might set things in order at the end of every shift, making sure that items are back where they belong before the next shift or next workday begins. People might shine equipment after every use so that it is ready for the next person who needs to use it.
The definition of who will do each needed activity, how to do the activity, and how often to do the activity will all be completed at the end of the standardize step. When the 5S duties are part of the regular work for people producing the product, the standardization becomes more possible.
Example checklist
Checklists are common tools produced in the standardize step, such as the sample daily checklist that follows:
Use standardize to eliminate steps
To further the standardization of the 5S system, it is also worthwhile to consider ways that you can make it impossible to need a particular step from sorting, setting in order, and shining.
For example, if you find that a table is likely to be moved that needs to be in a certain place, you might bolt the table in place. If test tubes need to be stored upside down so that they drain and dry after being washed, then you might get a rack that holds the tubes vertically while they dry.
Any activity that you can make unnecessarily or make impossible to do incorrectly helps to achieve the goals of 5S Lean thinking.
Sustain
While standardization describes how you will do the ongoing activities that achieve the first three parts of 5S Lean system, the sustain step is about the processes and systems that you develop so that you keep doing the activities laid out in the standardization step.
Different tools become popular in different contexts. In some organizations, daily walkthroughs and 5S audits are completed by supervisors to measure adherence to the activities outlined in the standardize step.
You might also see these ongoing checks incorporated into competitions or incentive programs to keep people invested in doing the 5S Lean methodology. It’s at this point that you really have a 5S system — a system that makes sure that your business continues to benefit from 5S Lean thinking.
Learn more
5S is only one of many useful Lean tools that you can use to improve your processes and businesses.
If you’re ready to learn more about Lean tools, check out GoSkills' Lean Six Sigma courses, designed to prepare you for certification with IASSC/PeopleCert.
Prepare to get certified in Lean Six Sigma
Start learning today with GoSkills courses
Start free trial